As a seasoned HVAC technician with two decades of hands-on experience, I have worked extensively with various brands of tankless water heaters. Among them, Navien distinguishes itself with its high-efficiency and reliable units. However, like any technology, these advanced appliances are prone to certain issues, often signaled through specific error codes. These Navien tankless water heater error codes are not just simple alerts; they are providing vital clues to underlying problems.
Understanding these Navien error codes is more than just a matter of identification; it involves a deep dive into the cause and the appropriate remedies. When a Navien tankless water heater displays an error code, it’s communicating a specific fault that needs attention.
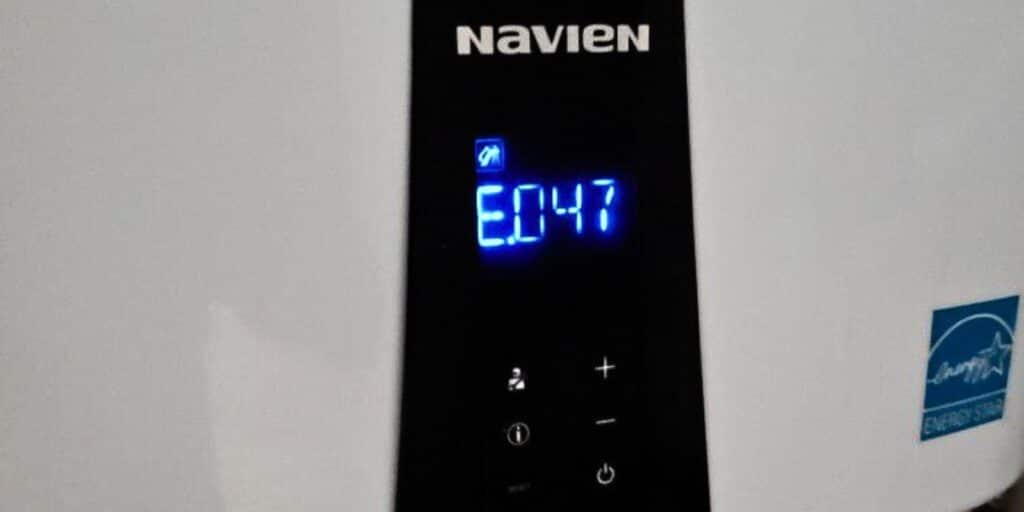
By understanding these codes and their associated troubleshooting steps, homeowners and technicians alike can address issues more effectively, ensuring the longevity and efficiency of their Navien tankless water heaters.
Common Navien Tankless Water Heater Error Codes
I’ve noted several common Navien error codes and how to fix them:
Error Code E001
Meaning: Indicates an ignition failure, potentially due to issues with the gas supply, a blocked or dirty air filter, or a damaged ignition device.
How to Fix/What to Check:
- Inspect the gas supply for any blockages or leaks.
- Check the air filter for blockage or dirt accumulation and clean or replace it.
- Examine the ignition device for damage and replace it if needed.
Error Code E002
Meaning: This signifies an overheating problem, possibly caused by a faulty temperature sensor or a clogged heat exchanger.
How to Fix/What to Check:
- Test the temperature sensor for functionality and replace it if it is defective.
- Inspect the heat exchanger for clogs and clean it thoroughly.
Error Code E003
Meaning: Indicates a circulation pump problem, which might be due to a faulty pump or wiring connection.
How to Fix/What to Check:
- Check the circulation pump for any signs of malfunction.
- Ensure all wiring connections to the pump are secure and in good condition.
Error Code E004
Meaning: Points to a flow sensor problem, possibly caused by a faulty sensor or wiring issues.
How to Fix/What to Check:
- Inspect the flow sensor for damage or malfunction.
- Verify the integrity of the wiring connections to the sensor.
Error Code E006
Meaning: Suggests a fan motor problem, potentially due to a faulty motor or wiring connection.
How to Fix/What to Check:
- Examine the fan motor for any signs of damage or wear.
- Check the motor’s wiring connections for any disconnections or damage.
Error Code E010
Meaning: Indicates an exhaust blockage or improper venting, possibly due to a clogged vent pipe or flue, insufficient ventilation, or incorrect installation.
How to Fix/What to Check:
- Inspect the venting system for blockages or improper installation.
- Ensure adequate ventilation according to the manufacturer’s guidelines.
Error Code E012
Meaning: Denotes a flame loss, which can be due to insufficient gas supply, low gas pressure, or a dirty burner.
How to Fix/What to Check:
- Check the gas supply and pressure to ensure they are within the required parameters.
- Clean the burner to remove any debris or buildup.
Error Code E013
Meaning: Indicates a thermistor problem, possibly caused by a faulty sensor or wiring connection.
How to Fix/What to Check:
- Test the thermistor for accuracy and replace it if needed.
- Examine and secure all related wiring connections.
Error Code E016
Meaning: Indicates a communication error between the circuit board and other components.
How to Fix/What to Check:
- Inspect the circuit board for signs of damage or malfunction.
- Check and secure all wiring connections between the circuit board and other components.
- If issues persist, consider replacing the circuit board.
Error Code E021
Meaning: Suggest a problem with the water inlet thermistor.
How to Fix/What to Check:
- Test the water inlet thermistor for proper functionality.
- Examine and secure wiring connections to the thermistor.
- Replace the thermistor if it is found to be faulty.
Error Code E022
Meaning: Indicates an issue with the outgoing water thermistor.
How to Fix/What to Check:
- Assess the outgoing water thermistor for correct operation.
- Check the wiring connections to the thermistor for any issues.
- Replace the thermistor if necessary.
Error Code E027
Meaning: Denotes an overvoltage problem, potentially caused by a power surge or faulty electrical components.
How to Fix/What to Check:
- Inspect the electrical system for signs of overvoltage or damage.
- Check for any faulty electrical components and replace them as needed.
- Ensure the unit is properly grounded and protected against power surges.
Error Code E029
Meaning: Indicates a problem with the air pressure sensor.
How to Fix/What to Check:
- Evaluate the air pressure sensor for any malfunction.
- Verify the integrity of the wiring connections to the sensor.
- Replace the sensor if it is defective.
Error Code E038
Meaning: Suggest an issue with the combustion chamber or flame rod.
How to Fix/What to Check:
- Clean the flame rod to remove any dirt or buildup.
- Inspect the combustion chamber for proper operation and cleanliness.
- Replace the flame rod if it is damaged.
Error Code E040
Meaning: Points to a problem with the air intake filter.
How to Fix/What to Check:
- Check the air intake filter for any clogs or dirt accumulation.
- Clean or replace the filter to ensure proper airflow.
Error Code E048
Meaning: Indicates an issue with the mixing valve.
How to Fix/What to Check:
- Inspect the mixing valve for any faults or damage.
- Ensure all wiring connections to the valve are secure and in good condition.
- Replace the mixing valve if it is found to be defective.
Error Code E055
Meaning: Suggest a problem with the heat exchanger.
How to Fix/What to Check:
- Examine the heat exchanger for any clogs or dirt buildup.
- Clean the heat exchanger thoroughly.
- Consider replacing the heat exchanger if cleaning does not resolve the issue.
Error Code E057
Meaning: Indicates a problem with the water pressure sensor.
How to Fix/What to Check:
- Test the water pressure sensor for accuracy and functionality.
- Check and secure wiring connections to the sensor.
- Replace the sensor if it is faulty.
Error Code E060
Meaning: Denotes an issue with the gas valve or regulator.
How to Fix/What to Check:
- Inspect the gas valve or regulator for proper operation.
- Examine wiring connections to the valve or regulator.
- Replace the gas valve or regulator if necessary.
Error Code E069
Meaning: Indicates a problem with the fan or fan motor.
How to Fix/What to Check:
- Check the fan and fan motor for any signs of malfunction.
- Ensure all wiring connections to the fan or motor are intact and secure.
Each of these Navien tankless water heater error codes provides a diagnostic starting point, guiding homeowners and technicians toward the right area of focus. Addressing these issues often requires a combination of inspection, cleaning, and part replacement. In many cases, especially when dealing with gas-related components or electrical wiring, it is advisable to seek the assistance of a professional HVAC technician to ensure safe and effective repairs.
Maintenance Tips to Prevent Future Issues
It’s essential to understand that regular maintenance is not just about preventing problems; it’s about ensuring the system’s efficiency, safety, and longevity. Here are more detailed Navien tankless water heater maintenance tips:
Annual Professional Servicing
Schedule an annual inspection and maintenance service with a qualified HVAC technician. This professional servicing should include the following:
- Gas Line Inspection: The technician will check for leaks and blockages and ensure the gas line is in optimal condition for safety and efficiency.
- Venting System Check: Proper venting is crucial for safe operation. The technician will inspect for any obstructions, damage, or installation issues.
- Electrical Component Evaluation: Since tankless water heaters rely on electrical components, a technician will inspect these for any signs of wear, damage, or loose connections.
Regular Self-Maintenance
- Filter Cleaning: Navien tankless water heaters have filters that need regular cleaning. Depending on your water quality and usage, this could be as often as every month. Clean filters ensure efficient operation and prevent problems related to water flow.
- Checking for Error Codes: Familiarize yourself with the common error codes and regularly check the system for these alerts. Early detection of issues can prevent major repairs.
- Water Pressure Checks: Regularly monitor water pressure, as extreme pressure can damage the unit. Installing a pressure-reducing valve might be necessary if the pressure is too high.
Seasonal Considerations
- Winterization: If you live in an area with freezing temperatures, ensure your unit is properly winterized to prevent freezing damage. This might include draining the unit or ensuring that it’s adequately insulated.
- Summer Checks: In warmer seasons, check for any dust or debris buildup, especially in the fan and vent areas, as these can hinder the unit’s performance.
Long-Term Care
- System Flushing: Depending on your water hardness, flushing the system to remove scale and sediment buildup is crucial. This is typically recommended annually but might be needed more frequently in areas with hard water.
- Anode Rod Inspection: If your model has an anode rod, inspect it periodically (usually during annual servicing) to prevent corrosion inside the tank.
Proactive Upgrades
- Software Updates: If your model supports it, ensure the software is up-to-date for optimal performance.
- Component Upgrades: Over time, some components might benefit from upgrades, especially if known issues or more efficient versions are available.
Documentation and Records
- Keep Records: Maintain a log of all services, repairs, and any issues encountered. This history is invaluable for troubleshooting and understanding the long-term performance of your unit.
In conclusion, understanding and addressing Navien tankless water heater error codes is essential for maintaining the longevity and efficiency of your heating system. While some troubleshooting can be done independently, don’t hesitate to seek professional assistance for complex issues. Regular maintenance is your best defense against these common problems.